why choose us
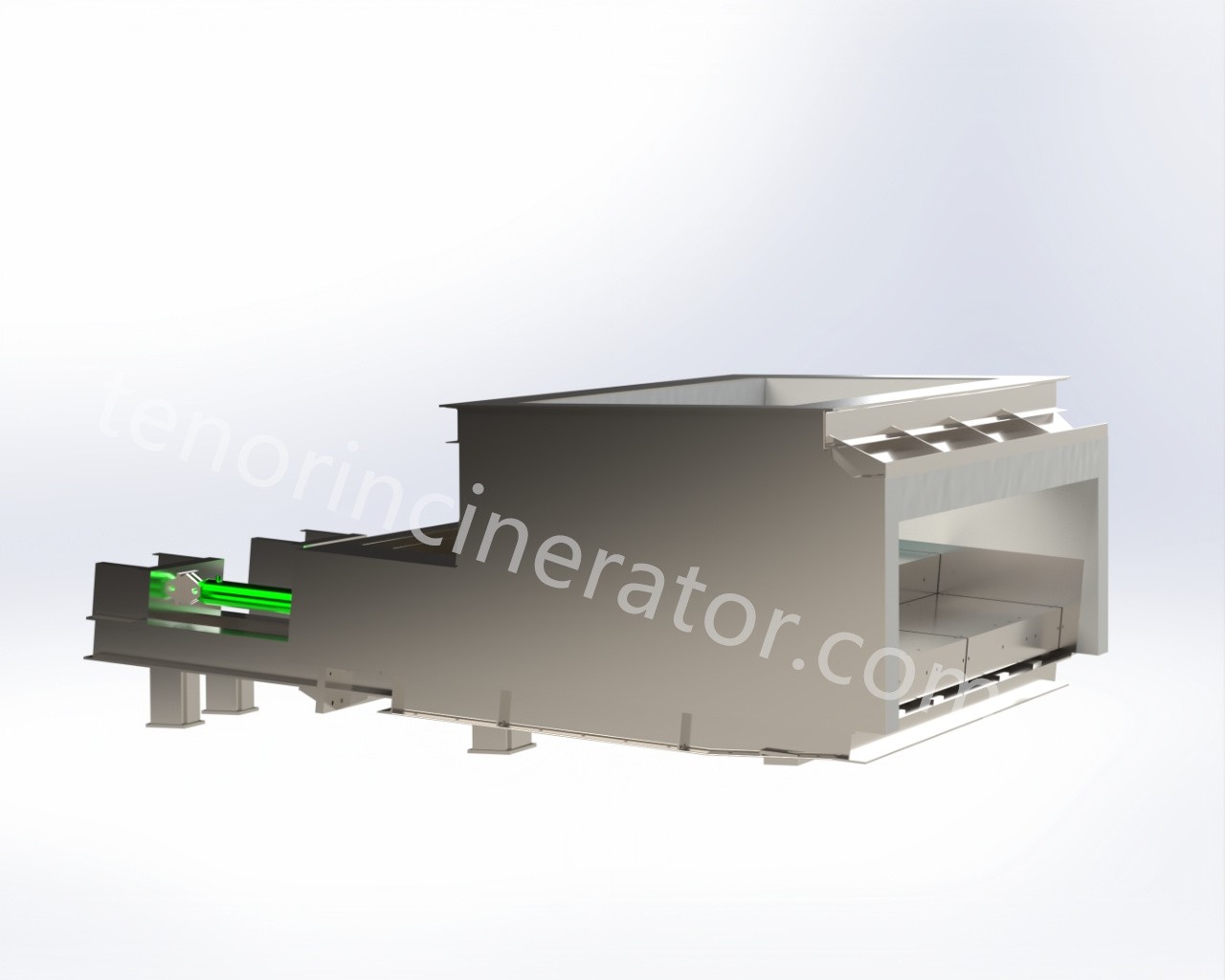
our products
The Fuel feeding system consists of a hopper and a feeder. There is a gate inside the hopper. The gate ensures sealing and taking into account the function of breaking the bridge. When the garbage clumps and builds bridges to block the hopper, the gate movement can be used to break the bridge. The hydraulic feeder and gate are driven by oil cylinders, and a certain amount of garbage is pushed into the incinerator through periodic reciprocating push and pull movements. The feeder can adjust the feeding speed according to the load of the incinerator.
The pusher of the garbage incinerator is a key component in the incineration process. There are three main types of pushers: reciprocating pushers, spiral pushers, and hydraulic pushers.
The reciprocating pusher moves garbage into the incinerator through a back-and-forth motion. It features a simple structure and convenient maintenance, making it suitable for small incinerators or situations with less garbage. Its advantages include stable pushing and high reliability, while its disadvantages are poor crushing and mixing of the garbage.
The spiral pusher utilizes rotating spiral blades to push garbage into the incinerator, offering continuous and uniform pushing. It is ideal for medium to large incinerators and for situations requiring high levels of garbage crushing and mixing. Advantages include a compact structure and small footprint, but it has high maintenance requirements and relatively poor adaptability to different types of garbage.
The hydraulic pusher uses a hydraulic system to drive a push plate that moves garbage into the incinerator. This type is characterized by its large thrust, fast speed, and long stroke, making it suitable for large incinerators or for garbage with special requirements, such as high viscosity and moisture content. Its advantages include strong adaptability and significant thrust, while its disadvantages include high equipment and maintenance costs.
A spiral pusher designed for large processing volumes, along with a centrifuge, includes a spiral pusher barrel and a spiral blade. A discharge section is integrated into the straight section of the barrel, with the discharge port arranged axially and evenly distributed around the circumference. This design addresses issues faced by existing horizontal screw centrifuges when handling large amounts of solid-liquid mixtures.
There are various manufacturing methods for the pusher device of the waste incinerator. One method involves preparing the materials, constructing the pusher mechanism and conveyor, then installing and testing the pusher device. Additionally, the pusher has a cooling structure, which includes a pusher box and a cooling mechanism. This setup dissipates heat through fan operation, enhancing the protection of the pusher assembly and extending its service life. A dust removal assembly is also included to maintain a clean working environment. The pusher in the crushing system is used for breaking down whole packages of tough fibers and hard materials, like rhizomes, fruits, and minerals, with the hydraulic pusher forcing materials into the cutting area, where the size of the crushed materials is controlled by screen apertures.
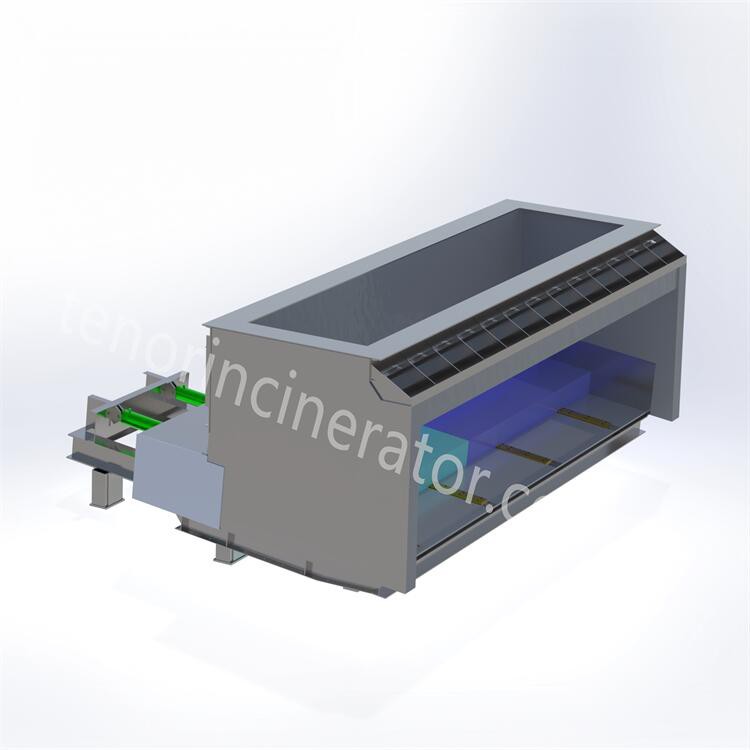
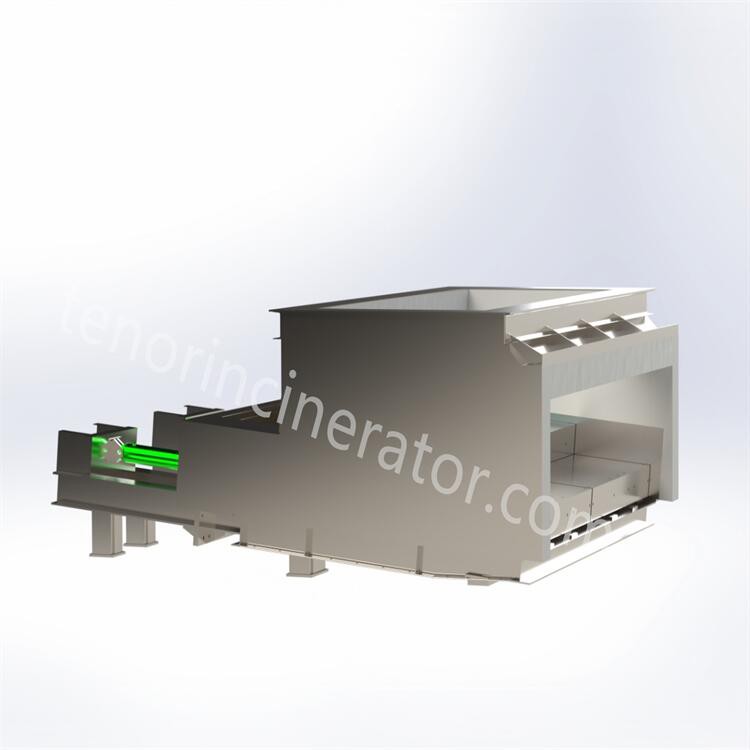
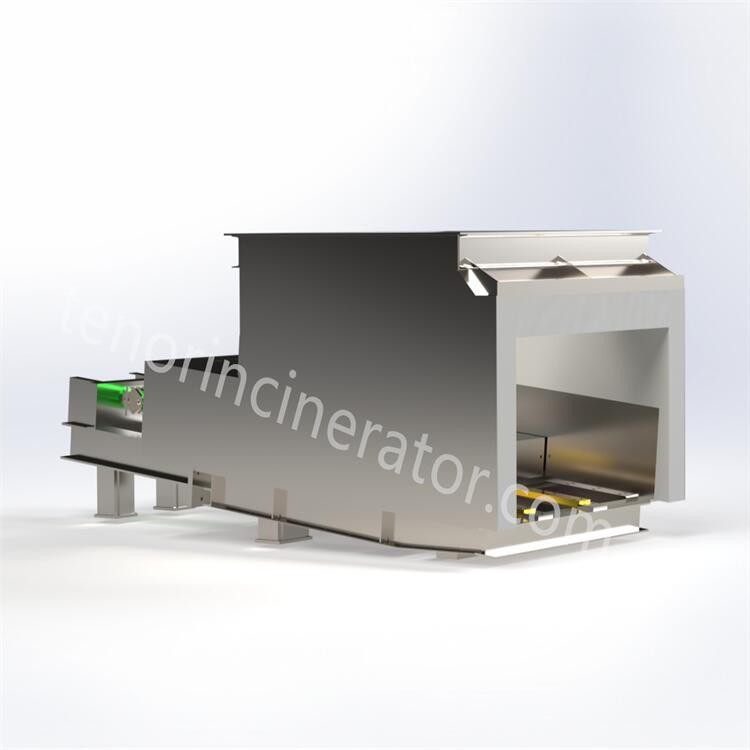
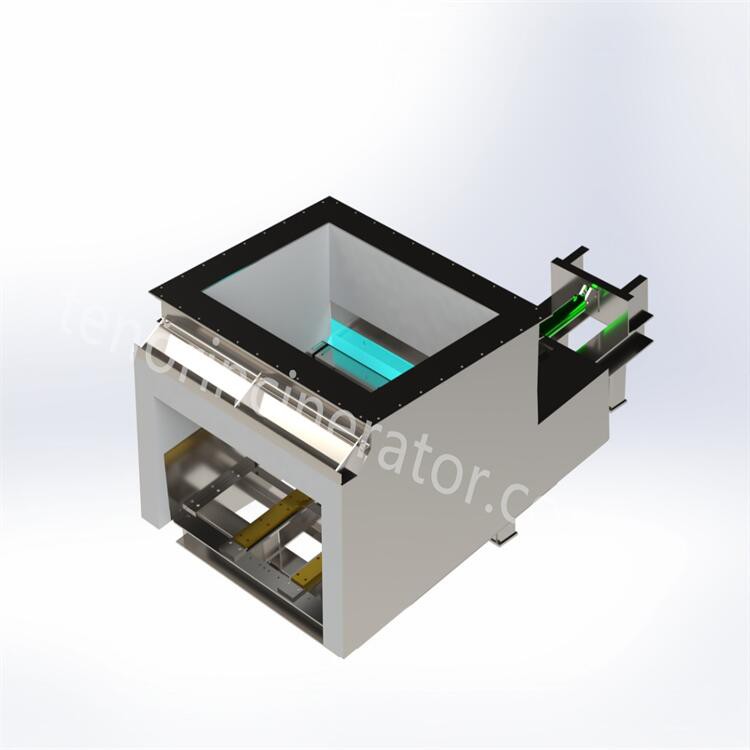
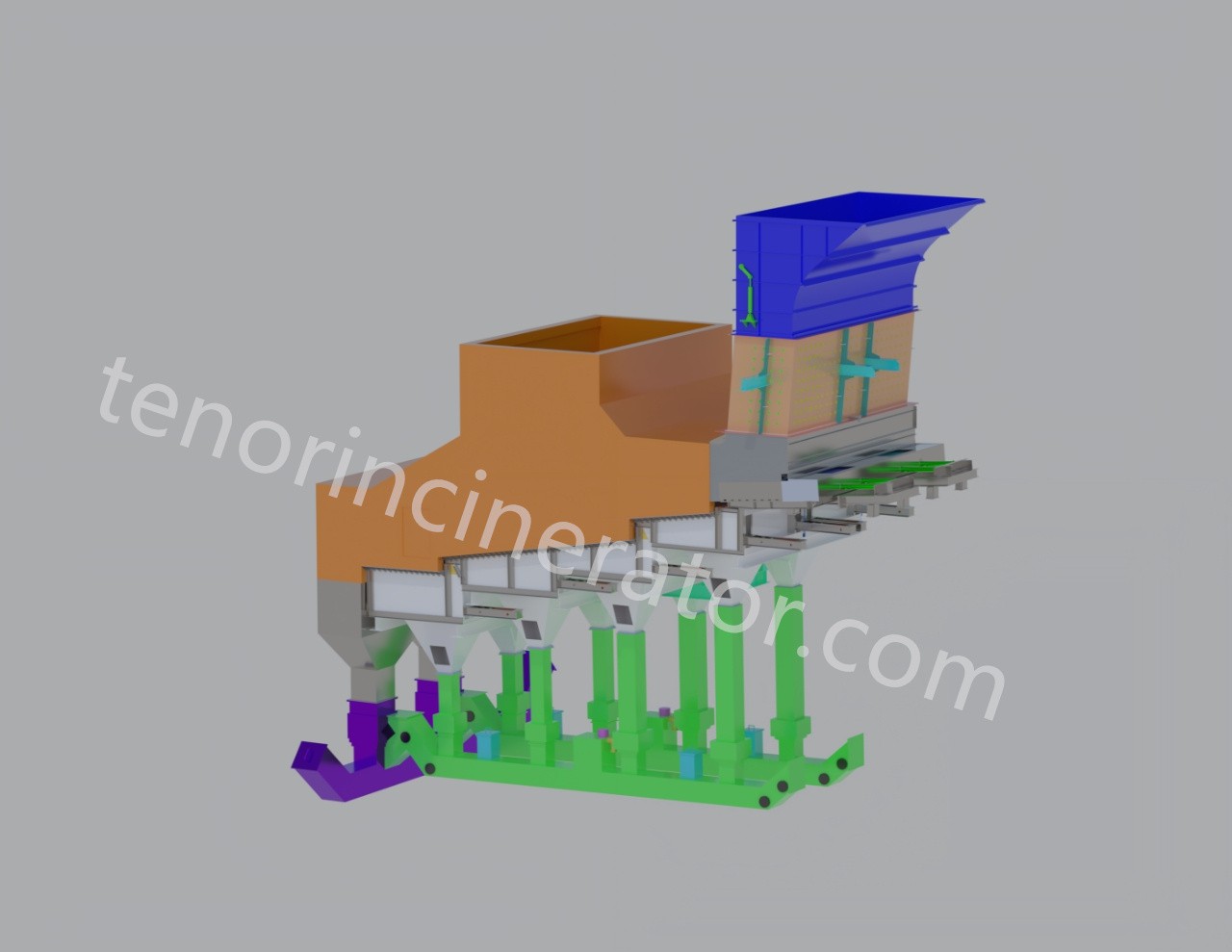
Can the pusher for the garbage incinerator be customized?
Differences in Requirements for Different Waste Incinerators
Size Adaptation: The models, specifications, sizes, and shapes of feed ports in waste incinerators vary significantly. For example, large waste incinerators require pushers with greater pushing capacity and size to handle large volumes of waste, while small waste incinerators need relatively smaller pushers with less pushing force. Custom pushers can be designed and manufactured according to the specific size requirements of the incinerator to ensure a perfect match, thus achieving efficient garbage pushing.
Structural Design: The internal structures and combustion processes of waste incinerators impose specific requirements on the structural design of pushers. For instance, the compact internal layout of some incinerators may necessitate pushers with special shapes or folding structures to operate smoothly in limited spaces. Additionally, incinerators that utilize specialized combustion technologies may require pushers to be specifically designed to connect with other components in the furnace, necessitating customized designs for the pusher structure.
Differences in Garbage Disposal Needs:
Garbage Type: There are many types of garbage, including domestic, industrial, and medical waste. These types vary significantly in shape, size, density, and moisture content. For example, industrial waste may contain large solid items that require the pusher to have strong thrust and a large push plate area, while medical waste, which often poses higher risks, requires pushers with appropriate protective measures and specialized pushing methods. Customized pushers can be optimized based on the characteristics of different types of garbage to improve disposal efficiency and safety.
Processing Volume Requirements: Different garbage disposal sites have varying requirements for processing volume. Large disposal plants may need to process significant amounts of garbage daily, necessitating pushers with high operational efficiency and large pushing frequencies. Conversely, smaller disposal stations or incinerators located in specific areas may have lower processing volumes, leading to reduced demands for the working intensity and frequency of the pushers. Customized pushers can be designed according to specific processing volume needs to ensure they meet the requirements of garbage disposal.
Special Functional Requirements:
Uniform Pushing Function: To ensure even burning of garbage in the incinerator, the pusher must provide uniform pushing. Some facilities may have stringent requirements for pushing uniformity, which necessitates customized designs for the push plate structure, pushing speed, and stroke to achieve precise and consistent pushing.
Anti-Stuck Function: During the garbage disposal process, blockages can occur, hindering the normal operation of the pusher. To mitigate this risk, some pushers need anti-stuck features, such as specially shaped push plates, vibration devices, or anti-stuck sensors. These functional requirements can be addressed through customization of the pushers.
main equipment
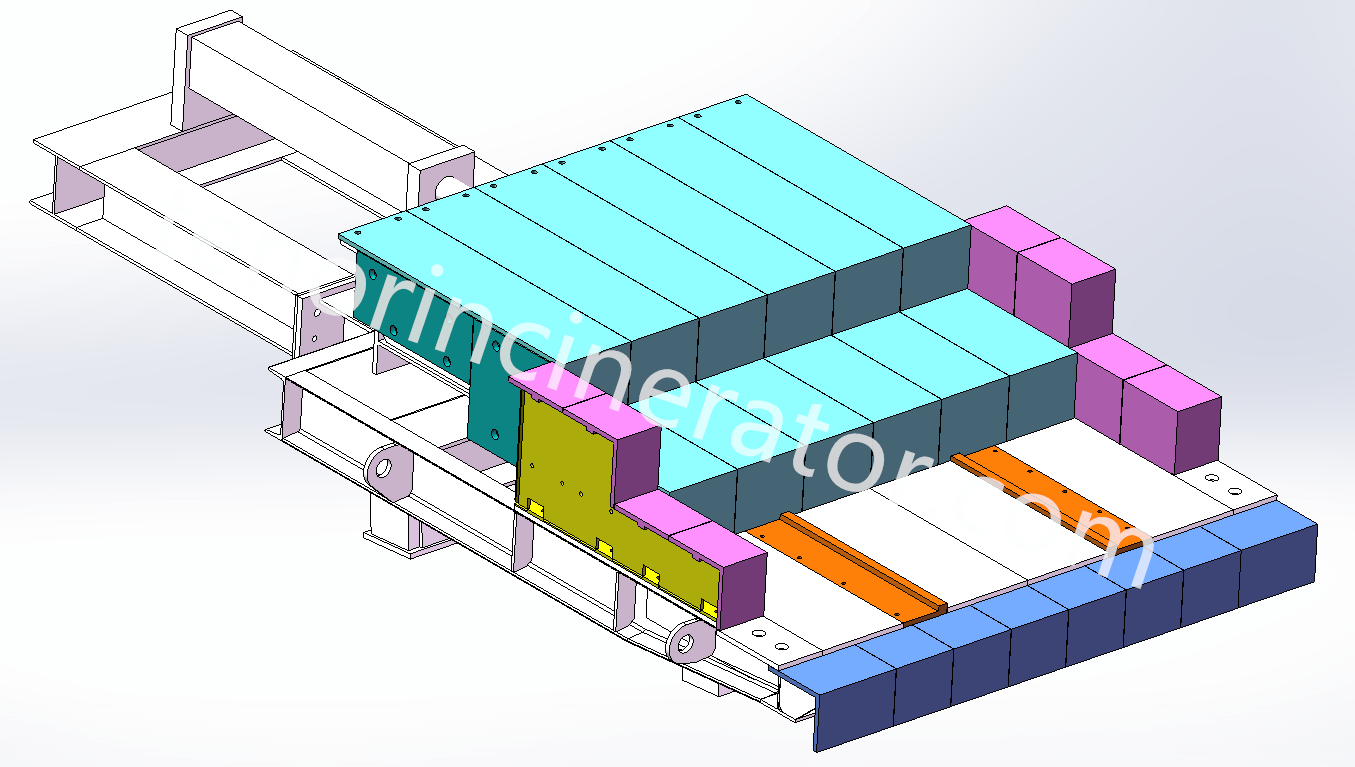
Hopper & feeder
Feeding system consists of hopper and feeder, hopper internal gate, the gate to ensure the sealing at the same time to take into account the function of breaking the bridge, in the garbage clusters bridge blocked hopper through the gate movement to realize the bridge. The feeder and the gate are driven by cylinders to push a certain amount of garbage into the incinerator through periodic reciprocating push and pull movements, and the feeder can adjust the feeding speed according to the load of the incinerator
Step Grate
Tenor garbage incineration grate is a downward-pushing stepped inclined reciprocating grate, the grate is divided into three stages of drying, combustion and burning out, and a height difference is set between each section of the grate, so that the garbage is scattered after falling and the garbage is pushed to move, and at the same time the garbage is prevented from gathering together to lead to incomplete combustion. The step grate is driven by hydraulic cylinders, and the three sections of the grate can be controlled independently, so that the movement cycle of the grate can be adjusted according to the combustion state in the furnace. The grate is made of heat-resistant cast steel, which has good wear-resistant, high temperature-resistant and corrosion-resistant properties..


Ash conveyor, slag remover
The ash system consists of an under-furnace ash hopper (cum air chamber), a horizontal ash conveyor, and a slag remover. The small amount of fine ash produced after complete waste combustion falls into the ash hopper through the grate gap and then collects in the horizontal ash conveyor. The main ash produced by waste combustion is pushed into the slag bucket through the grate of the combustion section, and then enters the wet slag remover together with the fine ash. All the ash is sent to
the slag pit by the slag remover.
Our Services - Cargo Loading Supervision and Securing
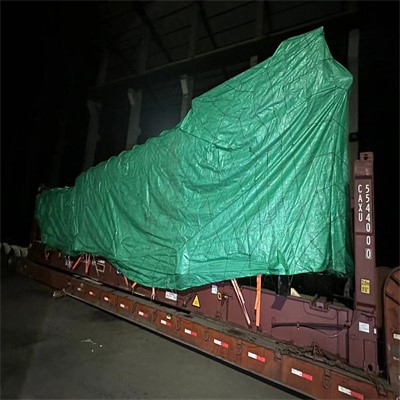

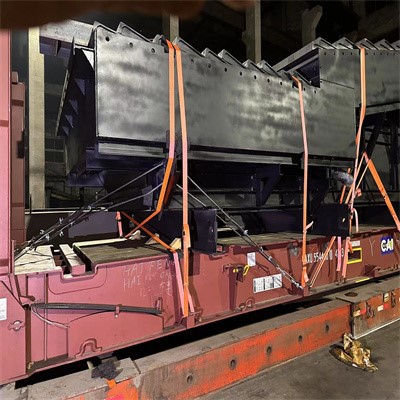
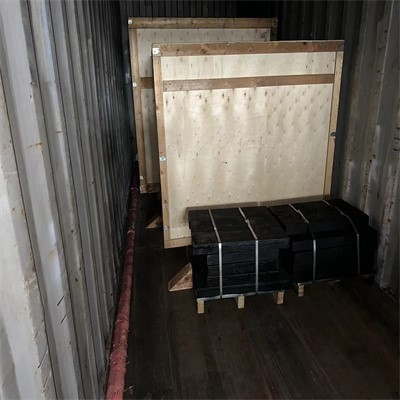
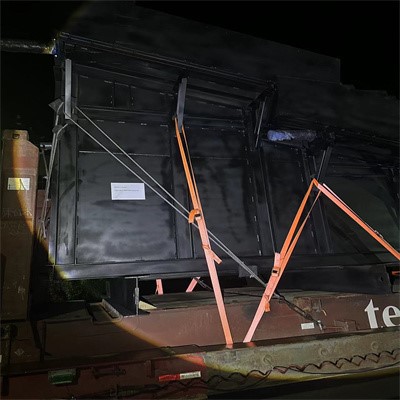
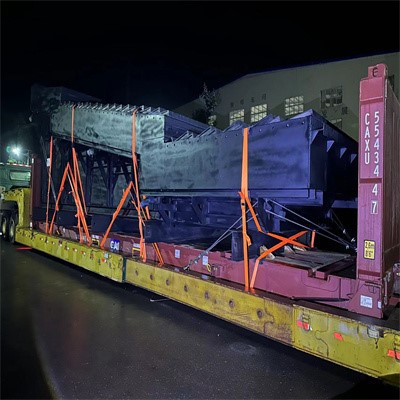
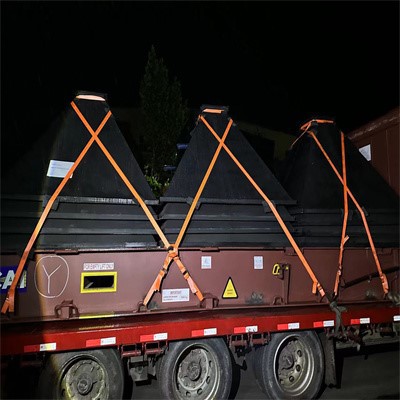