Incineration is a waste treatment process that involves the combustion of substances contained in waste materials. Industrial plants for waste incineration are commonly referred to as waste-to-energy facilities. Incineration and other high-temperature waste treatment systems are described as "thermal treatment".
Benefits of Industrial Garbage Incinerator
Wear resistance
During the operation of the waste incinerator, the waste residue will come into contact with the inner wall of the incinerator, which is easy to cause wear. Therefore, the material of the waste incinerator must have good wear resistance.
Corrosion resistance
In a high temperature and humid environment, the inner wall of the incinerator is prone to corrosion. Therefore, the material of the waste incinerator must have good corrosion resistance.
Good thermal conductivity
The waste incinerator needs to convert the heat of the fuel into steam, so it needs to have good thermal conductivity.
Good mechanical properties
The waste incinerator needs to withstand a high temperature and high pressure working environment, and the material must have good mechanical properties to ensure the stable operation of the equipment.
Introducing our small garbage incinerator – the perfect solution to managing small amounts of waste in an efficient and environmentally-conscious manner. Designed to fit seamlessly into any space, this compact incinerator features a robust construction, easy-to-use interface, and superior burn efficiency.
Our step grate incinerator utilizes an advanced combustion technology to efficiently dispose of waste materials. Designed to accommodate various types of waste, from municipal solid waste to medical waste, this incinerator's step grate system guarantees complete burn-out of the waste, producing minimal emissions and ash residue.
Waste Living Garbage Incinerator
Waste Living Garbage Incinerator is a facility designed to burn and dispose of waste materials such as household trash, industrial waste, and other non-recyclable materials. The incineration process involves the combustion of these materials at high temperatures, which reduces their volume and converts them into ash and gases.
Rural Garbage Incinerators are facilities designed to dispose of waste in rural areas where traditional waste management systems may not be readily available or practical.For rural areas, it's important that the incinerator design is robust, easy to maintain, and adaptable to different types of waste.
Our garbage incinerator grate is a reliable and efficient solution for managing waste. Made out of quality materials, our grate is designed to handle high temperatures and withstand the harsh conditions of incineration. It is perfect for incinerating large amounts of waste, ensuring quick and...
Garbage Incinerator for Solid Waste
Garbage Incinerator For Solid Waste are industrial waste disposal systems designed to reduce the volume of solid waste by burning it at high temperatures.
Garbage Incinerator for Household Waste
Our garbage incinerator for solid waste is a state-of-the-art solution for safe and efficient waste disposal. Designed to handle various types of waste materials, this incinerator utilizes advanced technology to incinerate solid waste and convert it into ash and gas, with minimal environmental impact.
Our household waste garbage incinerator is the perfect solution for the efficient and eco-friendly disposal of your daily trash. With a high-temperature combustion system, it is able to incinerate a variety of household waste products including plastics, paper, and food waste. It's compact design saves space and the user-friendly controls make it easy to operate.
Eco Friendly Garbage Incinerator
Introducing our compact garbage incinerator, designed to efficiently dispose of waste in a convenient and cost-effective manner. With its compact size, this incinerator is perfect for use in small spaces, while still offering a large capacity to handle a variety of waste types. Equipped with a state-of-the-art combustion system, our incinerator effectively incinerates waste, leaving behind only a small amount of ash.
Why Choose Us
Advanced equipment
We take strong measures to ensure that we use the highest quality equipment in the industry and that our equipment is regularly and meticulously maintained.
Rich experience
Has a long-standing reputation in the industry, which makes it stand out from its competitors. With over many years of experience, they have developed the skills necessary to meet their clients' needs.
Efficient and convenient
The company has established marketing networks around the world to provide high-quality services to customers in an efficient and convenient manner.
Quality assurance
In terms of quality assurance, the company strictly follows the standards and norms of the industry quality system. Adopt industry-leading testing equipment to ensure product quality and good reputation.
Professional team
We have a team of skilled and experienced professionals who are well-versed in the latest technology and industry standards. Our team is dedicated to ensuring that our customers get the best service and support possible.
Competitive prices
We offer our products at competitive prices, making them affordable for our customers. We believe that high-quality products should not come at a premium, and we strive to make our products accessible to all.
The principle of an incinerator is based on a two-stage combustion process, involving a primary combustion chamber and a secondary combustion chamber.
In the design of an incinerator, a primary combustion chamber is specifically intended for the burning of solid waste or sludge oil. This chamber is equipped with a primary burner, which initially receives diesel oil for ignition. Once ignited, the primary burner is then supplied with sludge oil, either manually or automatically, until it ignites. To facilitate effective combustion, the sludge burner receives atomizing air.
The amount of sludge entering the conversion chamber can be controlled through a pressure-regulating valve on the sludge return line.
When the heat from the primary burner is applied, solid waste will dry out and begin to burn, and the sludge oil may also catch fire. The gases produced during the primary combustion process proceed to the secondary combustion chamber. This secondary chamber is responsible for burning out any unburned exhaust gases to further minimize pollutants.
To separate the primary and secondary combustion chambers, a wall of ceramic heavy-duty refractory liners is installed. This division helps contain and control the combustion process within each chamber.
In cases where solid waste or garbage is being incinerated, it is fed into the incinerator through a feeding door. It is important to note that the primary burner cannot be ignited if this door is open. However, the rest of the combustion process continues as usual.
By employing the principle of a two-stage combustion process, with separate primary and secondary chambers, an incinerator ensures efficient and controlled burning of waste materials while minimizing the release of pollutants into the environment.
What Are the Precautions for the Maintenance of Garbage Incinerators
Regular cleaning
Regularly clean the residue and ash inside the incinerator to keep the furnace clean to ensure normal combustion effect.
Inspection and replacement
Regularly check the various components of the incinerator, such as transmission components, control system, etc., to ensure that they can operate normally.
Check the smoke exhaust system
Ensure that the smoke exhaust system is unobstructed to avoid smoke backflow or retention in the furnace due to poor smoke exhaust, which affects the combustion effect.
Check protective facilities
Regularly check and maintain protective facilities, such as temperature monitoring, pressure monitoring, alarm system, etc., to ensure that they can work normally in an emergency.
Fuel management
Use appropriate fuel and avoid using materials that do not meet the requirements to avoid damage to equipment or accidents such as fire and explosion. Regularly check the storage and use of fuel to ensure timely supply and reasonable use of fuel.
Lubrication and maintenance
Regularly lubricate and maintain bearings, gears and other components in the incinerator to reduce wear and friction and extend the service life of the equipment.
Record maintenance history
Record the history of each maintenance, including the maintenance date, maintenance content and replaced parts. This helps to track the maintenance of the equipment and detect potential problems in a timely manner.
Notes on long-term out-of-service
If the incinerator needs to be out of service for a long time, the main oil circuit and power supply switches should be turned off.
Industrial Waste Incinerator Market Overview
The Industrial Waste Incinerator Market size is expected to develop revenue and exponential market growth at a remarkable CAGR during the forecast period from 2023–2030. The growth of the market can be attributed to the increasing demand for Industrial Waste Incinerator owning to the Medical Waste Disposal, Chemical Waste Disposal, Municipal Solid Waste Disposal, Hazardous Waste Disposal, Electronic Waste Disposal Applications across the global level. The report provides insights regarding the lucrative opportunities in the Industrial Waste Incinerator Market at the country level. The report also includes a precise cost, segments, trends, region, and commercial development of the major key players globally for the projected period.
The Industrial Waste Incinerator Market report represents gathered information about a market within an industry or various industries. The Industrial Waste Incinerator Market report includes analysis in terms of both quantitative and qualitative data with a forecast period of the report extending from 2023 to 2030. The report is prepared to take into consideration various factors such as Product pricing, Product or services penetration at both country and regional levels, Country GDP, market dynamics of parent market & child markets, End application industries, major players, consumer buying behavior, economic, political, social scenarios of countries, many others. The report is divided into various segments to offer a detailed analysis of the market from every possible aspect of the market.
The overall report focuses on primary sections such as – market segments, market outlook, competitive landscape, and company profiles. The segments provide details in terms of various perspectives such as end-use industry, product or service type, and any other relevant segmentation as per the market' s current scenario which includes various aspects to perform further marketing activity. The market outlook section gives a detailed analysis of market evolution, growth drivers, restraints, opportunities, and challenges, Porter' s 5 Force' s Framework, macroeconomic analysis, value chain analysis and pricing analysis that directly shape the market at present and over the forecasted period. The drivers and restraints cover the internal factors of the market whereas opportunities and challenges are the external factors that are affecting the market. The market outlook section also gives an indication of the trends influencing new business development and investment opportunities.
Preparing the incinerator
Ensure that the incinerator is in proper working condition, with all necessary maintenance and safety checks performed. Verify that the primary and secondary combustion chambers are clean and ready for operation.
Preparing the fuel
If required, ensure that the primary burner is supplied with the initial ignition fuel, such as diesel oil. This fuel is used to ignite the primary burner and initiate the combustion process.
Starting the incineration process
Ignite the primary burner using the initial ignition fuel. Once the primary burner is ignited, switch to the sludge oil as the primary fuel source for the combustion process. Monitor the ignition process to ensure that the sludge oil ignites properly.
Adjusting combustion parameters
To facilitate effective combustion, provide atomizing air to the sludge burner. This helps optimize the burning of sludge oil and ensures efficient incineration.
Controlling sludge input
Utilize the pressure-regulating valve on the sludge return line to control the amount of sludge entering the conversion space. Adjust the valve as needed to maintain the desired sludge input for optimal combustion.
Combustion in primary chamber
The heat generated by the primary burner will cause the solid waste to dry out and begin burning. Simultaneously, the sludge oil will ignite and contribute to the combustion process. The primary combustion chamber' s design, including its transmission area, aids in the drying and burning of solid waste.
Secondary combustion chamber
The gases produced in the primary combustion chamber proceed to the secondary combustion chamber. The unburned exhaust fumes are burned off in this chamber to ensure complete combustion and minimize pollutants. The primary and secondary combustion chambers are separated by a wall of ceramic heavy-duty refractory liners.
Waste feeding
In the case of solid waste or garbage, feed the waste into the incinerator through the feeding door. It is essential to ensure that the feeding door is closed during the combustion process to prevent interference with the primary burner. However, the rest of the combustion process continues as usual.
Monitoring and safety checks
Continuously monitor the combustion process, ensuring that the incinerator is functioning correctly and safely. Regularly check for any abnormalities, leaks, or malfunctions that may affect the combustion or safety of the incinerator.
Shutting down the incinerator
Once the incineration process is complete or when the waste feeding is finished, follow the appropriate shutdown procedure. This may involve extinguishing the primary burner, allowing the system to cool down, and performing necessary cleaning and maintenance tasks.
Parts of Incinerator
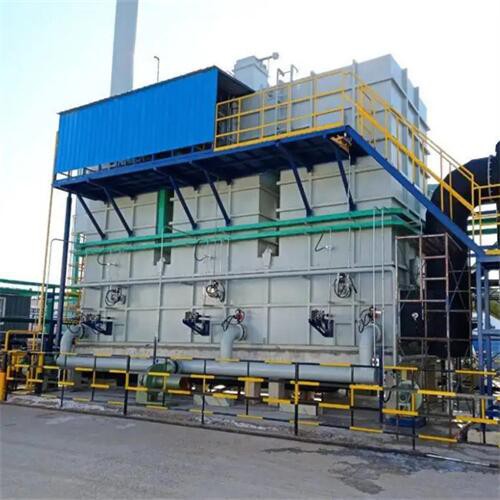
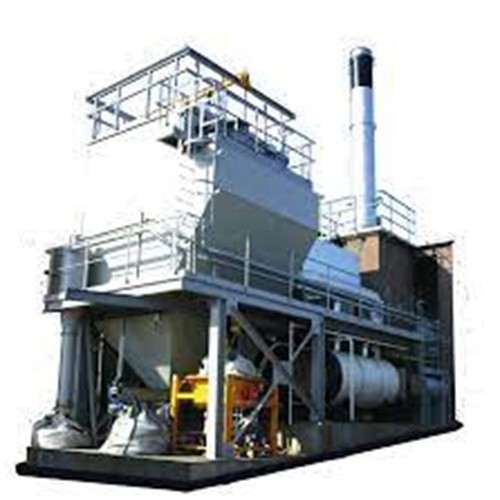
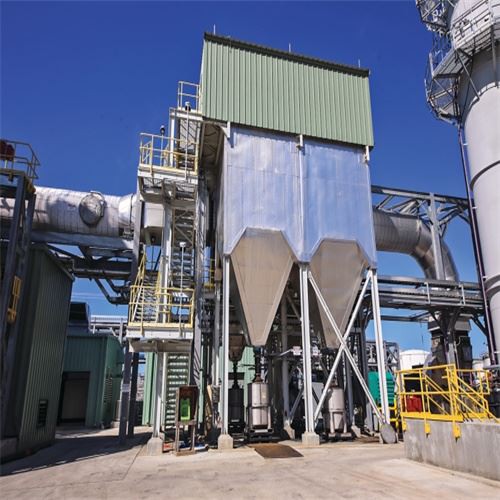
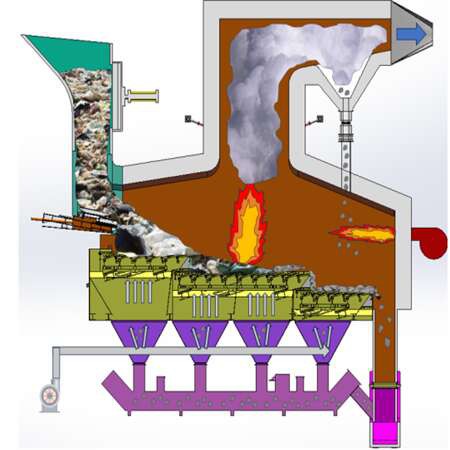
Primary chamber
All garbage will be fed into the primary chamber and burned for the first time there. The primary chamber is where the waste vapourises. The low air-to-fuel ratio in this starved-air chamber causes the waste to dry out and makes it easier for it to evaporate, burning up most of the carbon.
Secondary chamber
Waste-derived volatile/gasified substances are transferred to the secondary chamber. To complete combustion, more air is injected in the second stage into the volatile gases created in the initial chamber. Temperatures in the secondary chamber are higher than those in the primary chamber. Due to the appropriate residence time, high temperature, and 100% surplus air in the secondary chamber, the gaseous products (volatile material) are oxidized. The gases are handled after they exit the secondary chamber.
The gases are introduced to the droplet separator, where the moisture is taken out of the gases. This lowers the temperature of the flue gas, making it safe to release into the atmosphere.
Flue Stack
The term ''chimney' ' also applies to the flue stack. Stack height requirements for most incinerators are 3 meters or greater. In more populated places or where the atmosphere requires it, this requirement will be greater.
Control panel and thermocouples
These regulate the machine' s operation and guarantee that the chambers are heated up before any waste is loaded for incineration. Depending on the type of waste, the settings can be tailored to the operator' s needs.
Burners
These are utilized to warm the incinerator up and are often turned off throughout the burning process.
Fuel tanks
The fuel is kept in storage. During the operation of the incinerator, the burners will have direct lines into the tank.
Applications of Incinerator
Medical waste
Medical wastes generated from laboratories, hospitals, and health clinics can pose health risks if not properly treated or disposed of. Incinerators are designed to destroy and neutralize medical waste.
Animal waste
Incinerators are employed to dispose of animal wastes, including carcasses, waste, and byproducts, thereby preventing the spread of infection and viruses.
General waste
General wastes include less harmful wastes from sites such as mining, small communities, and military operations, which must be destroyed to reduce environmental impact. Thus, incinerators are devised to incinerate such wastes.
Nanomaterial wastes
Incinerators are utilized to dispose of nanomaterial wastes such as consumer products in municipal solid waste, wastes from nanotechnology research and development, hazardous wastes, etc.
Top Incinerator Emissions Control Technologies
Selective Non-Catalytic Reduction (SNCR)
Ammonia or urea injection to react with and neutralize nitrogen oxide gases, preventing their release. Up to 60% NOx reduction.
Dry Sorbent Injection (DSI)
Injects powdered activated carbon to adsorb mercury, dioxins, and acid gases. Also, hydrated lime to capture sulfur and chloride gases. Achieves 95%+ acid gas neutralization.
Baghouse Fabric Filters
Multicompartment fabric filter houses actively filter particulate matter from flue gas flows through high-efficiency (~99.5%) filtration bags. Fly ash is captured for disposal.
Wet & Dry Electrostatic Precipitators (ESPs)
Dry and wet electrostatic scrubbers apply high voltage discharge wires to impart electrical charge on particles, which are then captured on grounded collection plates for removal.
Selective Catalytic Reduction (SCR)
Final stage, flue gas passes over a catalyst bed, converting nitrogen oxides into nitrogen, carbon dioxide, and water vapor, achieving 90%+ NOx destruction removal efficiency.
Our Factory
Tenor Low Carbon new Energy Technology (Liaoning) Co., Ltd. was established in 2021 and registered at the Industrial Incubation Base of Dalian University of Technology. Through cooperation with thermal power departments, environmental departments, mechanical departments, inorganic materials and other disciplines of HIT and Dalian University of Technology, the company focuses on designing and developing complete sets of small urban waste incineration technologies; Focusing on the application of technologies such as furnace arches, modular assembly, and dust reduction and dioxin removal inside the furnace to ensure full combustion of waste.
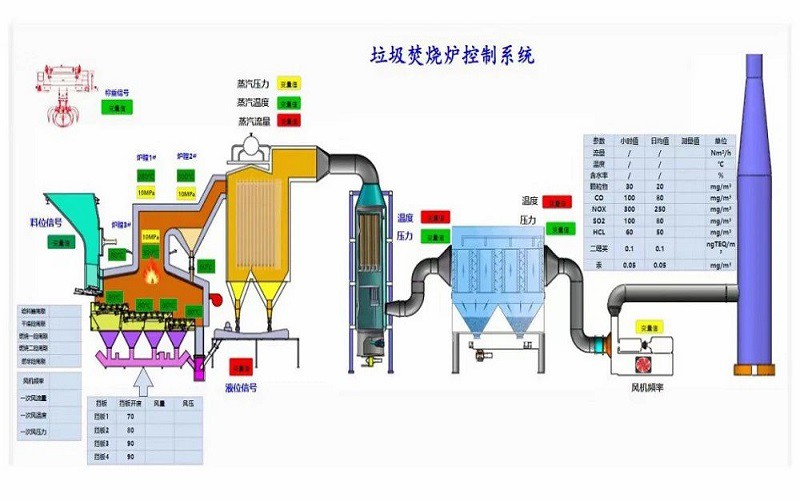
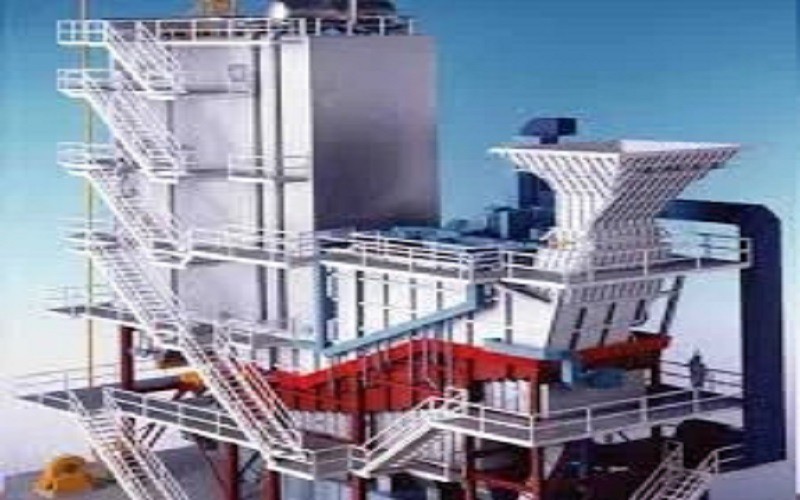
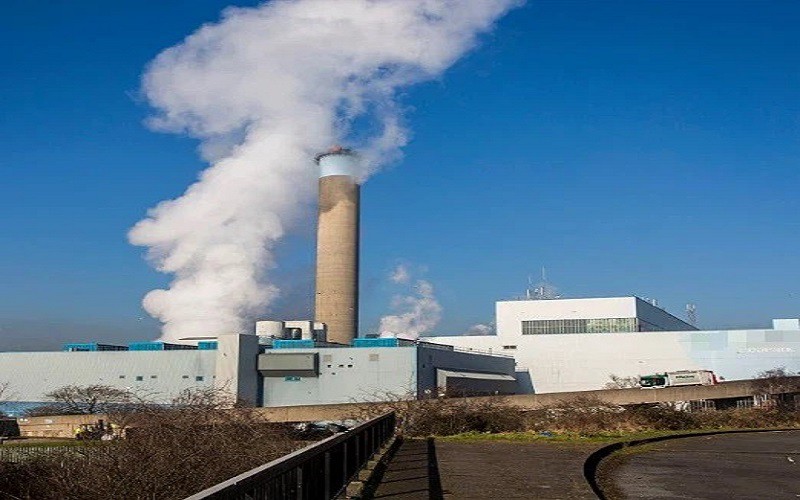
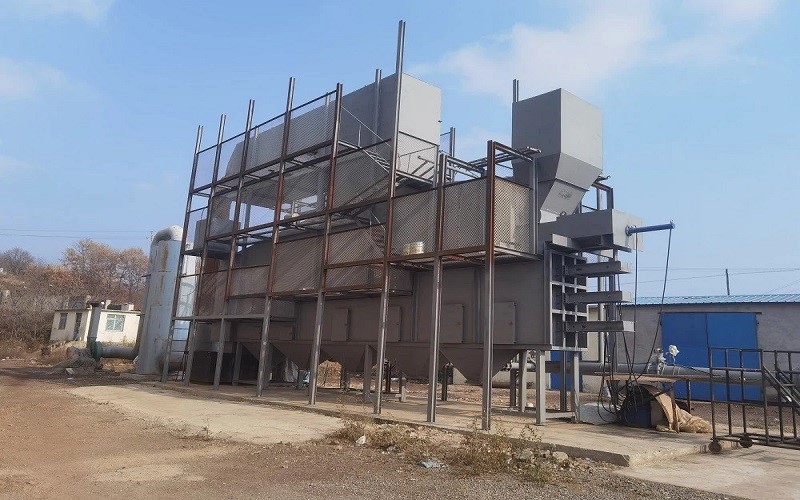
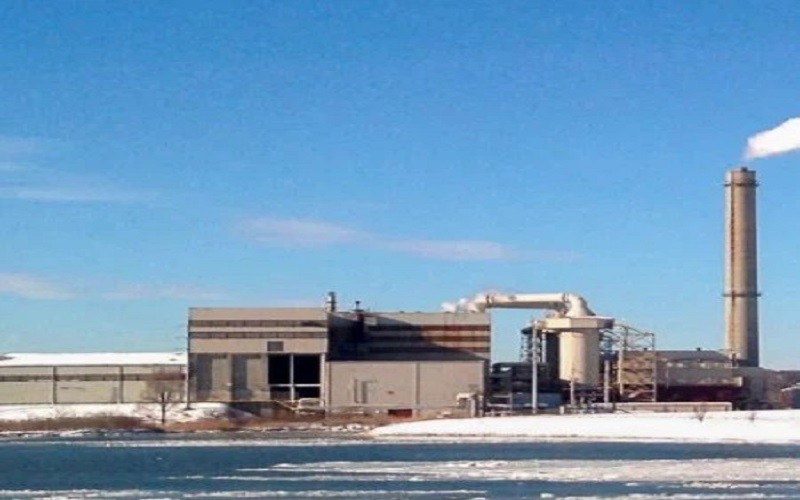
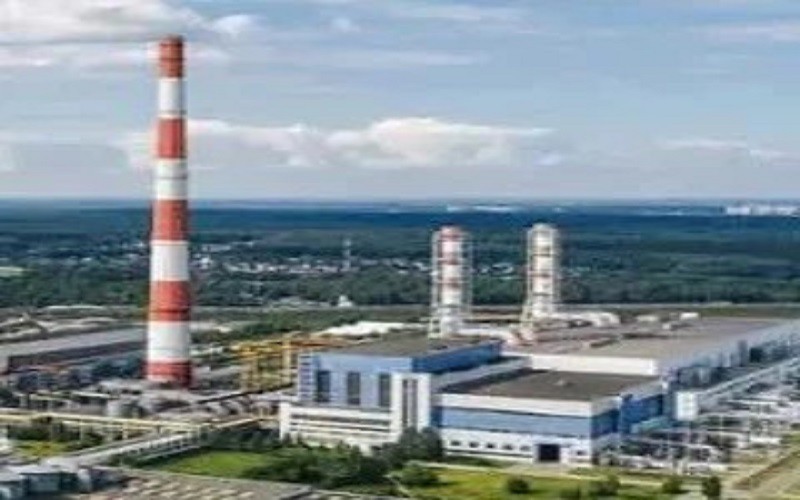